Organosilicone Potting Silicone Rubber Compounds for PCB
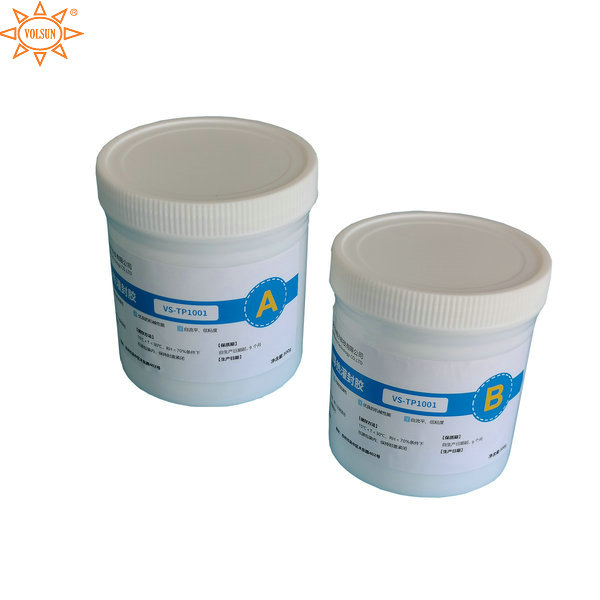
Description
VS-TP2001 is a two-component 1:1 type heat-curing silicone thermally conductive potting compound that cures at room temperature or after heating to form an elastic thermally conductive silicone rubber, specially designed for the manufacture of electrical and electronic products and modules, such as high Potting protection of power supply modules, frequency converters, sensors, etc., connection and fixation between automotive electronic devices and PCB, etc.
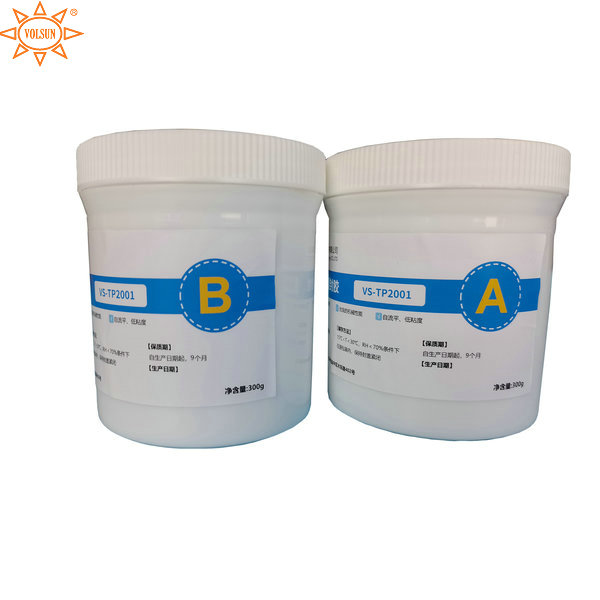
Features
- Continuous operating temperature:-70℃~+200℃
- Excellent mechanical properties and extensibility
- Excellent thermal conductivity and aging resistance
- Low viscosity, self-leveling, excellent drilling ability
- Low modulus, low stress, good adhesion to both metals and plastics
Technical Performance
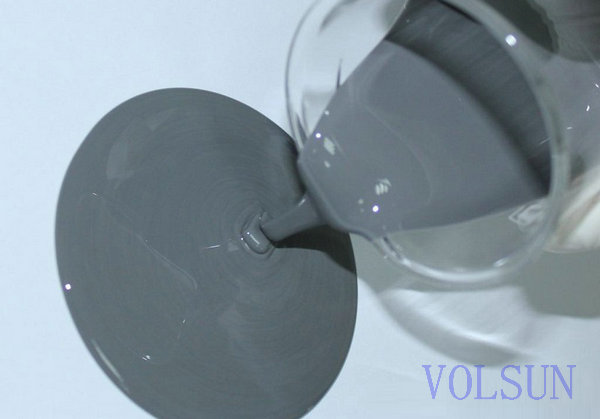
Dimension
Instructions
1. A and B components are stirred separately
2. Mixing the well-stirred components A and B according to the ratio of 1:1 (volume ratio/weight ratio can be used) well
3. The mixed compound is poured into the device which need to be sealed, then static curing (Can be cured at room temperature or by heating)
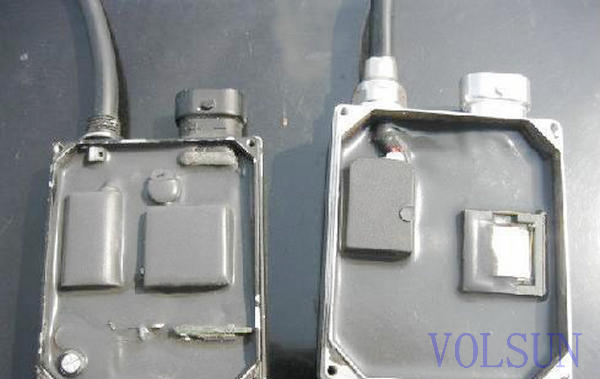
Precautions
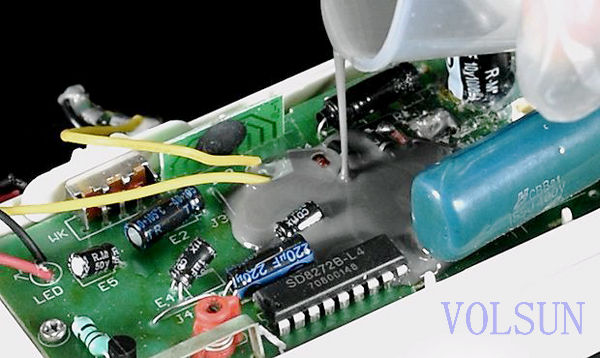
Storage conditions & Shelf life
1. The product should be stored in the original packaging, keeping the lid tightly closed to avoid contamination (Temperature: 15℃<T<30℃; Relative Humidity: RH<70%)
2. Shelf life is 9 months from the date of manufacture
Welcome to contact with us if any needs via volsun2006@szvolsun.com
Item | Typical Data | Test Method |
Mixing ratio | 1:1 | / |
Color(After mixing) | Grey | Visual |
Viscosity (Component A) @25℃ | 5500±500cps | ASTM D2196 |
Viscosity (Component B) @25℃ | 5500±500cps | ASTM D2196 |
Viscosity (After mixing) @25℃ | 5500±500cps | ASTM D2196 |
Opening hours @25℃ | ≥90min | / |
Initial setting time @25℃ | 50-60min | / |
Curing condition | 30min/50℃;20min/100℃ | / |
Thermal Conductivity | 2.0±0.2 W/m·k | ASTM D5470 |
Thermal resistance | 0.000815m2·k/W | ASTM D5470 |
Hardness | 35±5 Shore A | GB/T 531.1-2008 |
Density | 2.3 g/cm3 | GB/T 1033.1-2008 |
Tensile strength | 200KPa | GB/T 528-2009 |
Elongation at break | 12% | GB/T 528-2009 |
Flame retardance | V-0 | UL94 |
Breakdown strength | ≥10 kV/mm | GB/T 1695-2005 |
Volume resistivity | ≥ 1.0×1014 Ω·cm | GB/T 1692-2008 |
Dielectric constant(1000Hz) | 4.7~5.5 | GB/T 1693-2007 |
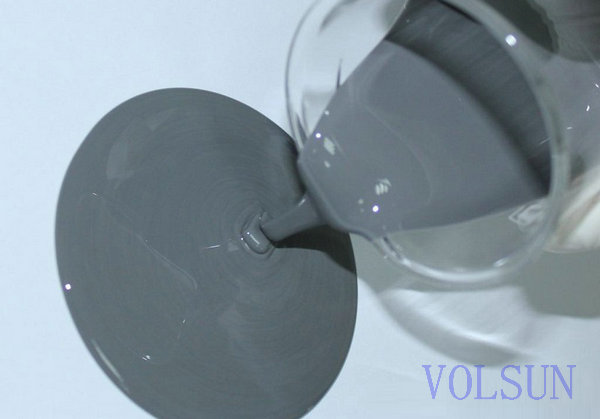
Dimension
Size | Package |
VS-TP2001(1kg) | Component A: 0.5kg; Component B: 0.5kg |
VS-TP2001(20kg) | Component A: 10kg; Component B: 10kg |
VS-TP2001(40kg) | Component A: 20kg; Component B: 20kg |
VS-TP2001(80kg) | Component A: 40kg; Component B: 40kg |
VS-TP2001(100kg) | Component A: 50kg; Component B: 50kg |
Note: The special sizes & packages are available on request.
Instructions
1. A and B components are stirred separately
2. Mixing the well-stirred components A and B according to the ratio of 1:1 (volume ratio/weight ratio can be used) well
3. The mixed compound is poured into the device which need to be sealed, then static curing (Can be cured at room temperature or by heating)
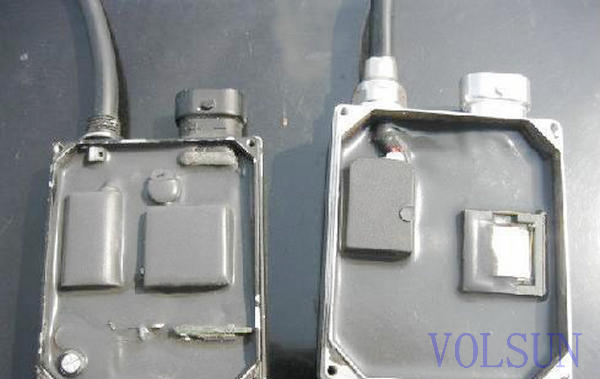
Precautions
- In order to ensure the uniform distribution of fillers, components A and B must be stirred separately before mixing, so that each compounding agent is evenly mixed.
- After A and B are mixed, they will react and cure each other, so they need to be used up after mixing and they cannot be used twice after mixing and curing.
- When pouring into the protective part, there should be no large debris or other contaminants in the protective part to avoid affecting the mutual adhesion of the material and the object
- Before the material is fully cured, avoid other objects contacting the material, affecting the appearance and protective performance of the material
- This product should not be in the mouth and eyes. If it accidentally enters the mouth and eyes, rinse it with water in time or go to the hospital for medical treatment.
- If need high thermal conductivity, vacuum degassing is required before pouring
- In low temperature environment, the curing time will be extended accordingly
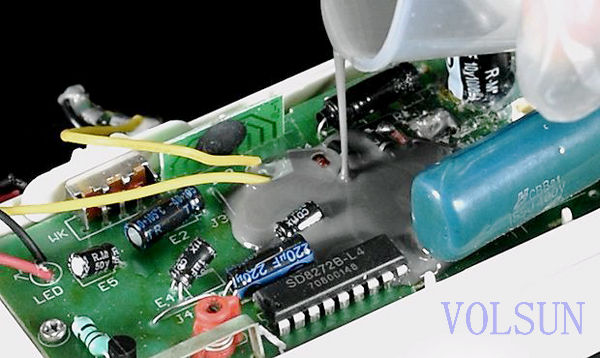
Storage conditions & Shelf life
1. The product should be stored in the original packaging, keeping the lid tightly closed to avoid contamination (Temperature: 15℃<T<30℃; Relative Humidity: RH<70%)
2. Shelf life is 9 months from the date of manufacture
Welcome to contact with us if any needs via volsun2006@szvolsun.com
- CONTACT TEL: +86-512-66386808
- SALES CONTACT: volsun2006@szvolsun.com